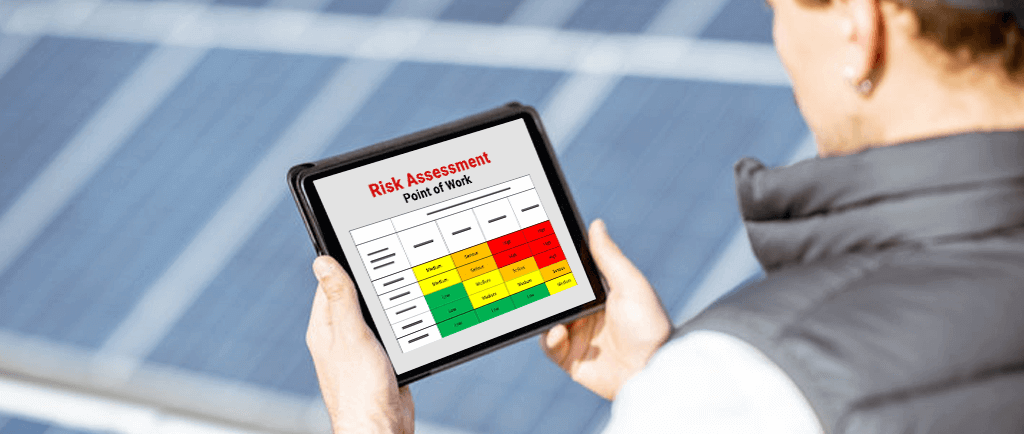
What is Point of Work Risk Assessment (POWRA) in Safety?
Point of Work Risk Assessment, or POWRA, is our safety playbook’s critical player. It’s all about stepping into a workspace with vigilance, identifying risks that are unique to that moment and place. This isn’t your average look at hazards; POWRA zeroes in on the present, adapting safety measures as conditions evolve. It’s like weaving a safety net on the spot, tailored to catch any unforeseen risks as we navigate through our day.
Perfect for dynamic environments where unpredictability is the only constant, POWRA stands as the agile hero of workplace safety. It keeps workers safeguarded and regulators satisfied, marking a game-changing approach to preventing accidents. Let’s dive deeper into how this superhero operates and why it’s revolutionizing safety standards.
Analyzing the importance of POWRA
The importance of POWRA in ensuring workplace safety cannot be overstated. Let’s break down why it’s such a game-changer:
Immediate Risk Identification:
Imagine the work site as a living, breathing entity that changes from day to day, even hour to hour. POWRA empowers workers to identify risks that pop up in real-time, right before the work kicks off. It’s like having the ability to see around corners, ensuring no new hazard slips through unnoticed.
Dynamic Work Environments:
In places where the only constant is change, POWRA is the steadfast guardian. Whether it’s a construction site morphing with each added beam or a manufacturing floor adapting to new production lines, POWRA ensures safety protocols evolve in lockstep with the work environment.
Legal and Compliance Aspects:
Beyond keeping workers safe, POWRA helps businesses stay on the right side of health and safety regulations. It’s the shield against compliance breaches, ensuring that safety isn’t just a priority but a fundamental practice.
Related read: Our listing of the best Health and Safety Software.
Steps to Conduct a POWRA
Conducting a POWRA might seem daunting, but it boils down to a straightforward process. Here’s how to tackle it effectively:
1. Prep Work: Before anything, gather all necessary information about the task at hand. Understand the work environment, the tools needed, and the potential hazards that might be lurking.
2. Hazard Hunt: With prep work done, it’s time to play detective. Identify any and all hazards associated with the task. Look for the obvious and not-so-obvious risks, keeping the work environment and operations in mind.
3. Risk Rating: Now, put on your analyst hat. Assess the identified hazards for their potential impact and the likelihood of occurrence. This step helps prioritize which risks need immediate attention.
4. Control Measures: Armed with your risk assessment, devise strategies to mitigate these risks. This could range from eliminating the hazard entirely to introducing safety equipment or changing work processes.
5. Document and Communicate: Write down everything. The identified hazards, their assessed risks, and the control measures decided upon. Share this information with everyone involved in the task.
6. Review and Update: Remember, a POWRA is not a one-and-done deal. It’s a living document that needs to be reviewed and updated as conditions change or as new information comes to light.
Best Practices for POWRA
To make your POWRA as effective as possible, here are some best practices to keep in mind:
Involve the Team: Safety is a team sport. Involve workers in the risk assessment process. Their hands-on experience can provide invaluable insights into potential hazards and effective controls.
Train and Educate: Ensure everyone involved understands how to conduct a POWRA and why it’s important. Knowledge is power, especially when it comes to safety.
Adapt and Update: Work environments and tasks evolve; your POWRA should too. Be ready to adapt and update the assessment as new information comes in or as the situation changes.
Prioritize Communication: A POWRA is only as good as the communication around it. Ensure the findings and control measures are clearly communicated to all relevant parties.
Foster a Safety Culture: Encourage a workplace culture where safety is everyone’s priority. A strong safety culture supports the effective implementation of POWRA and ensures its success.
Understanding the trio: POWRA, JSA and HIRA
Navigating the safety landscape, it’s essential to understand the distinct tools at our disposal. Let’s decode how POWRA, JSA, and HIRA differ, yet complement each other in ensuring workplace safety:
POWRA: The Agile Scout
POWRA specializes in the here and now, offering a snapshot of risks at the moment work is about to commence. It’s the agile scout, quickly assessing the terrain for immediate hazards. This nimbleness makes it ideal for environments where conditions can shift unexpectedly, ensuring safety measures are as current as the task at hand.
JSA: The Detailed Strategist
Job Safety Analysis, or JSA, takes a step back to examine each task within a job, dissecting it into steps to identify potential hazards. It’s the meticulous planner, crafting a detailed strategy for safe task execution. JSA is about understanding the dance between worker, tool, and environment, choreographing a safe performance from start to finish.
HIRA: The Big-Picture Analyst
Hazard Identification and Risk Assessment, or HIRA, zooms out even further. It surveys the entire landscape of potential hazards across a workplace or process. HIRA is the big-picture analyst, identifying everything from physical to chemical hazards, ensuring nothing escapes the safety net, no matter how broad.
Alternative names to POWRA
The concept of Point of Work Risk Assessment (POWRA) might be known or referred to by different names across various industries, reflecting the specific focus or terminology preferred within those fields. While the core idea remains the same—assessing risks at the point and time of work—here are a few alternative names or similar concepts:
1. Dynamic Risk Assessment (DRA): Often used in emergency services or industries where conditions can change rapidly, DRA emphasizes the need for ongoing risk assessment during the course of work.
2. Last-Minute Risk Assessment (LMRA): Similar to POWRA, LMRA is a quick, final check done right before starting a task, focusing on any risks that might have been overlooked or that have changed.
3. Field Level Risk Assessment (FLRA): Used primarily in industries like Construction and Oil and Gas, FLRA focuses on assessing risks at the specific location or field where work is being performed.
4. Pre-Task Planning (PTP): While PTP is broader and includes aspects like resource allocation and scheduling, it also involves identifying and mitigating risks before work begins.
5. Safety Moment or Safety Pause: This is a brief, informal safety meeting before the start of a task or shift, where workers discuss potential hazards and safety measures. While not a formal risk assessment, it serves a similar purpose in promoting situational awareness and safety.
6. Tailboard or Toolbox Talks: Toolbox talks are short safety meetings held on-site before work begins. Though often used for communication and training, they can include elements of risk assessment related to the day’s tasks.
These variations reflect the adaptability of the concept to different operational and cultural contexts within industries. Despite the differences in terminology, the underlying principle is consistent: to proactively identify and mitigate risks immediately before commencing work, ensuring the safety of all involved.
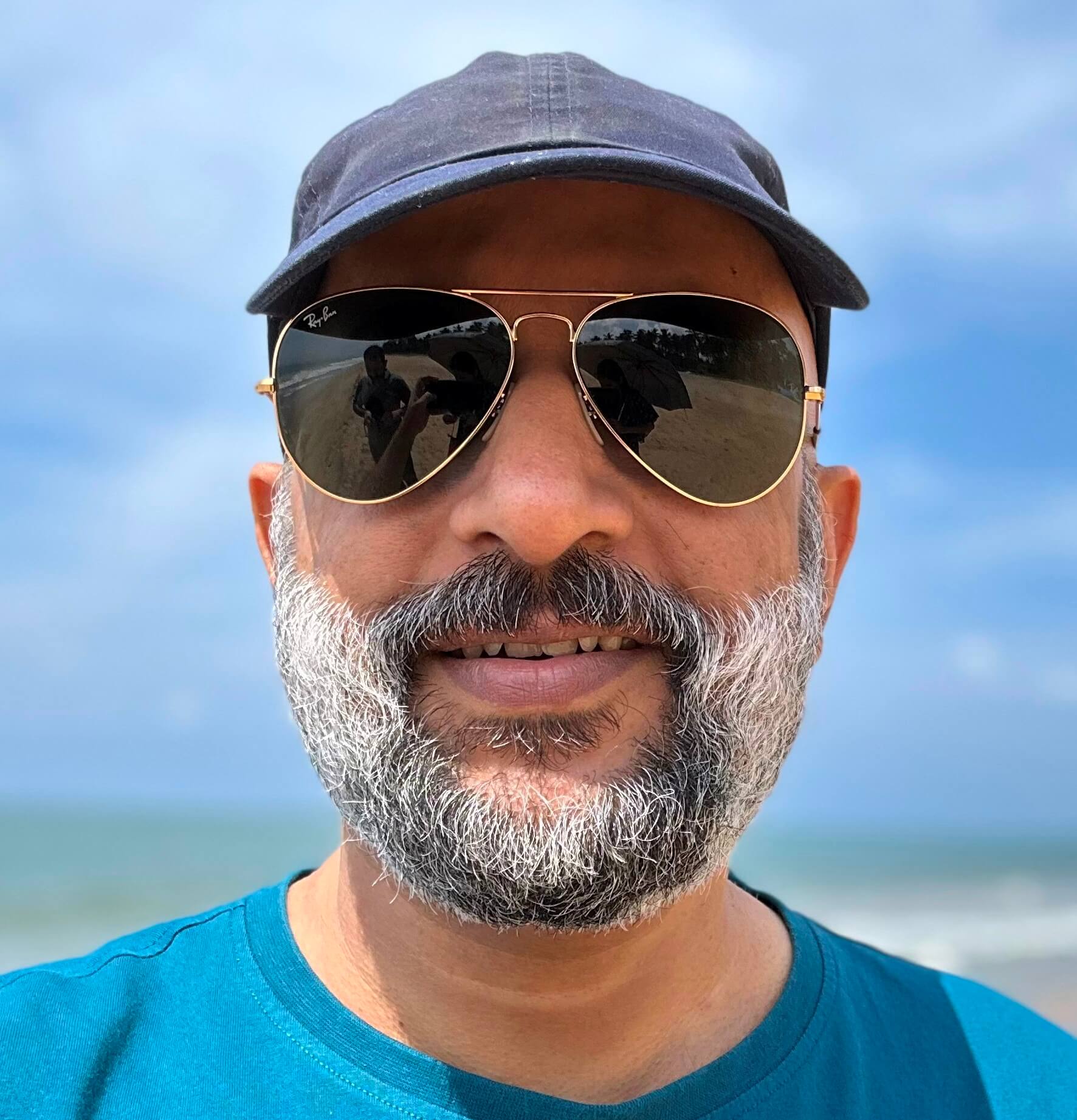
Ramesh Nair is the Founder and Principal Partner of Niyati Technologies, the company behind Safetymint.
He’s a dedicated advocate for workplace safety. Ramesh firmly believes that every individual deserves to return home safely after a day’s work. Safetymint, the innovative safety management software, emerged from this conviction. It’s a platform designed to streamline safety management, empower safety professionals, and enhance safety in workplaces.
Through his blog, Ramesh shares insights, best practices, and innovative solutions for workplace safety. Visit his social media profiles to follow him for regular updates.